At this point, it should be called the industrial evolution.
Yes, the industrial revolution was a historical period of innovation in the manufacturing and selling of goods, the impacts of which reverberated into every aspect of the economy, but it’s not as if these transformational innovations have stopped.
In fact, the most recent innovations in technology, software, robotics, and more are driving the fourth major transformational change in the evolution of manufacturing. It is known as Industry 4.0 — or the fourth industrial revolution.
What is Digital Transformation in Manufacturing?
Digital transformation in manufacturing is the integration of technologically modernized equipment like smart sensors, the industrial internet of things (IIoT), and other edge devices, which are components that connect on-site machinery to the broader network, passing real-time data to machine learning models and software to increase efficiencies.
We use the term “edge device” broadly because insightful data is being collected and processed from robots in the factory to reps in the field.
The most intuitive impact on efficiencies is the increased throughput of production but digitalization in manufacturing is impacting a whole host of processes. From 3D renderings in product design to sales and customer service automation. Digital transformation is being felt throughout the entire organizational hierarchy, from the factory floor to the C-suite.
Digital Transformation’s Impact on Manufacturing
When viewed from a high level, digital transformation in manufacturing may appear to be as singular and simple as factories having an internet connection. However, digital transformation goes much deeper and is more widespread.
1. Industrial Internet of Things (IIoT)
An internet-connected factory floor is a simple, yet revolutionary idea, and having each device in the assembly line connected helps identify, predict, and prevent bottlenecks.
Examples of IIoT devices include smart sensors to detect maintenance requirements, RFID chips to monitor inventory levels, drones equipped with computer vision algorithms to identify abnormalities, and more.
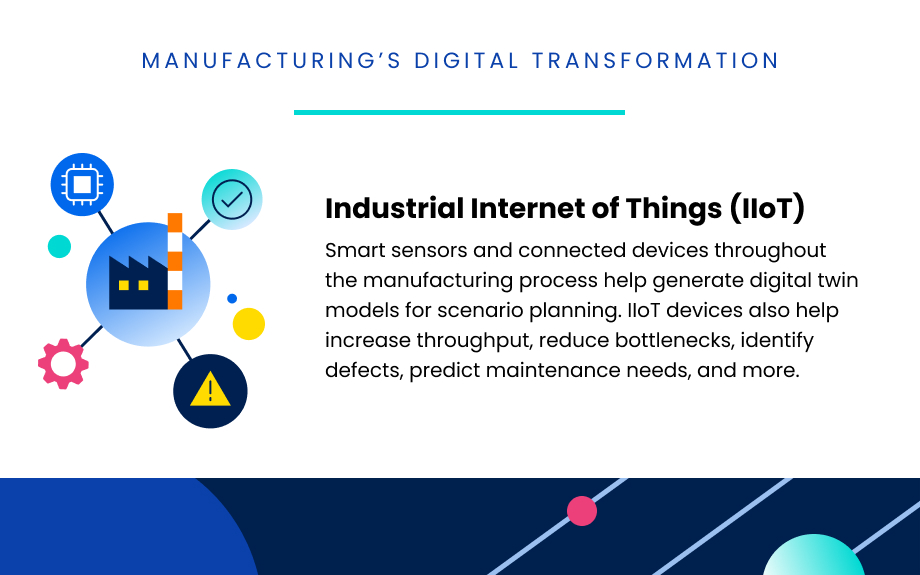
2. Robotics in Manufacturing
Just like mechanical looms igniting fears among the Luddites of the textile industry, autonomous robots are top of mind for the modern machinist. Innovations in robotics provide a similar positive impact that the loom did by increasing safety, productivity, and new opportunities for roles and responsibilities.
The adoption of industrial robots, driven largely by the automotive industry, has increased by 300% in the last decade. Thankfully, many manufacturers are reaping the benefits of pairing a robot and a human together to collaborate on the task at hand. This powerful partnership between man and machine will help accelerate digital transformation in the manufacturing process.
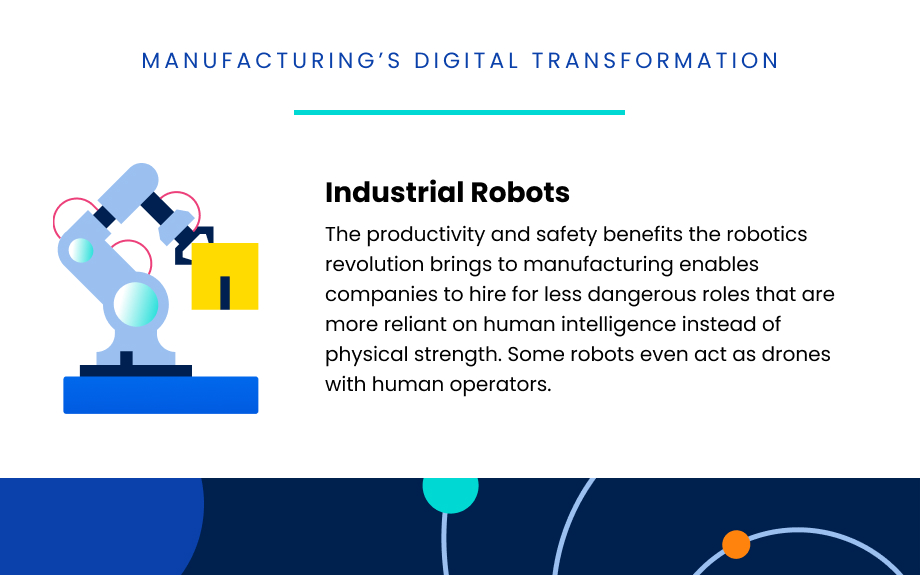
3. Automation
Productivity is important in nearly every line of work, but in manufacturing, productivity is the whole point. Manufacturers have long relied on automation to increase productivity, but automation can only be relied upon to a point since humans are still exclusively capable of handling certain tasks.
In manufacturing’s digital transformation, machine learning models are proving proficient in automating, or augmenting, the tasks of humans. For example, computer vision models can now flag defects in production for human review. While humans are still an important resource in the manufacturing process, automation is becoming more pervasive in production every year.
Robotic process automation (RPA) is the process of automating repetitive tasks in business operations, sales, marketing, and more. It’s the equivalent of automated robots in the factory, but for the front office.
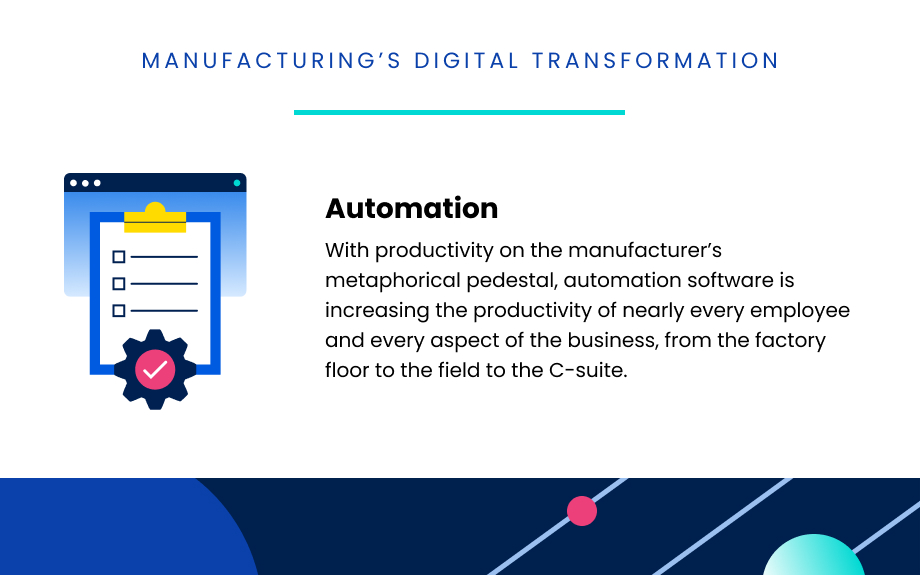
4. AR, VR, and Other Wearables
Clay Christensen, the author of multiple best-selling books on disruptive technology, argues that truly transformational technology usually gets its start as a toy. Examples of this include augmented reality, virtual reality, and wearables.
Today, AR and VR are becoming influential tools in the manufacturing process. CAD models for designing new parts, products, or processes have historically been viewed in 2D before being produced in 3D. AR glasses now enable engineers to visualize, inspect, and modify a 3D model before investing the time and money to manufacture a product.
As the world moves towards a future in the metaverse, manufacturing is one of the industries leading the charge in early adoption. The metaverse will allow human operators to be mentally present in the factory while extracting their physical presence away from this sometimes dangerous environment. From simulation to surveillance, the metaverse offers immense opportunities to further reduce costs and improve productivity.
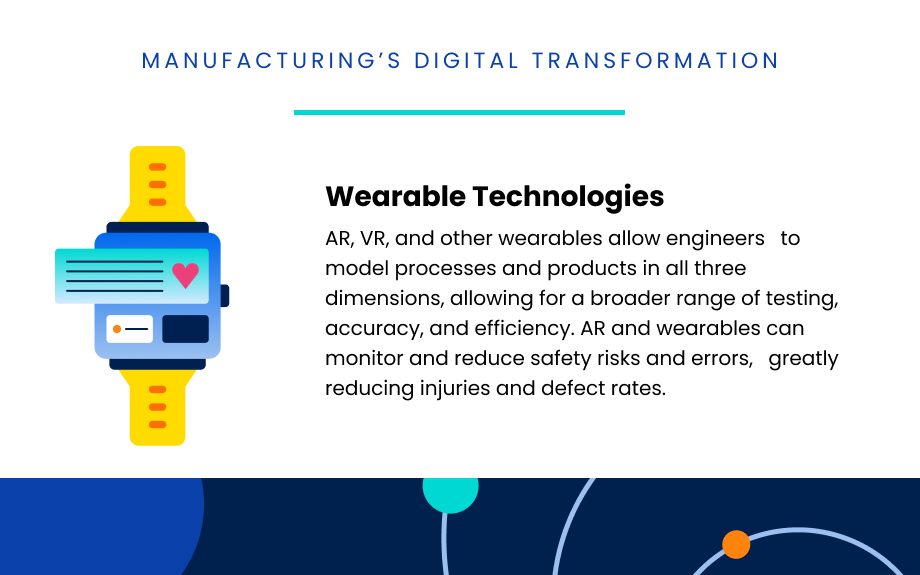
5. Supply Chain Planning & Reassessment
Since 2020, the global supply chain has experienced ongoing constraints as raw material and labor shortages met geopolitical and economic complexities, making it a ripe target for digital disruption.
Supply and demand forecasting using machine learning, for example, is becoming a vital component of logistics planning. Accurate forecasts give companies the ability to route individual orders to factories based on a number of factors including inventory levels, proximity to the customer, and more.
Real-time inventory tracking updates eCommerce platforms to prevent customers from purchasing sold-out products, which reduces customer support costs.
Recently, supply chain management has been disrupted by blockchain technology and smart contracts. While simultaneously establishing a single source of truth for transactions, trust, and security, this technology also offers the ability to create a digital twin of your current network.
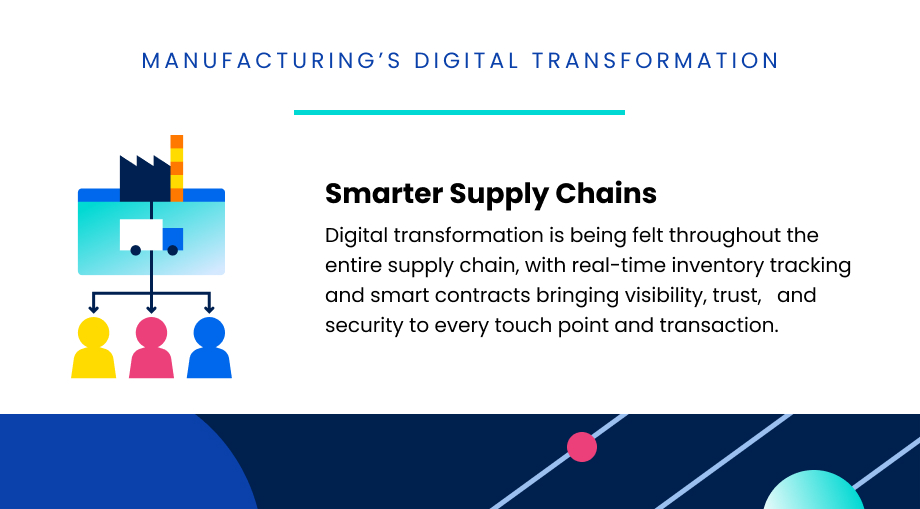
6. Real-World Machine Learning and AI
AI is a loaded acronym these days, but modern AI provides novel solutions to problems that have historically been reserved for humans. This includes everything from image recognition and segmentation models able to parse product images for defects to text analysis in deal correspondence and the accurate prediction of revenue growth.
As the industrial evolution continues and we move in the direction of AGI (artificial general intelligence), more and more problems will be feasibly solved by self-supervised deep learning, where AI improves performance without additional human input.
It’s worth noting that most AI researchers agree that we are nowhere near the singularity (where artificial intelligence surpasses human intelligence), but no one would deny the progress made over the last decade has been enlightening and empowering for every industry, especially manufacturing.
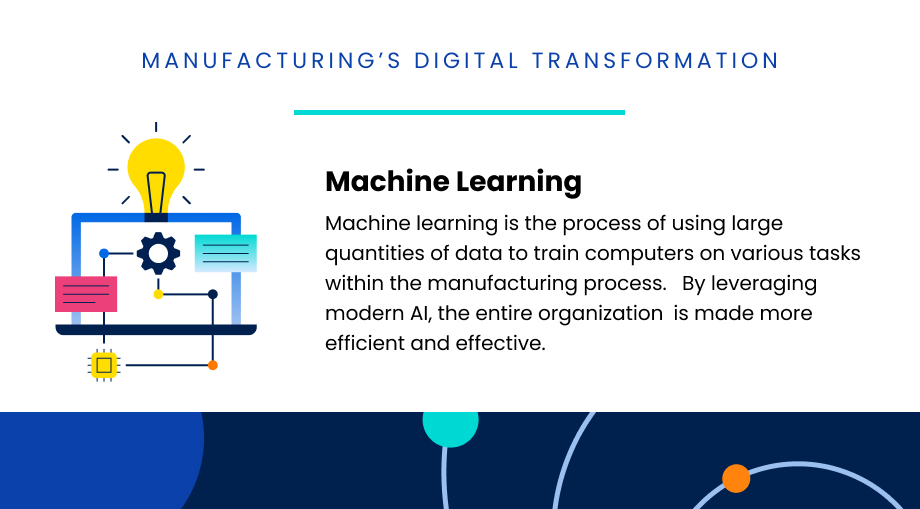
5 Tips for Supercharging Digital Transformation
We’re currently undergoing a period of disruption unlike any other in history. The rapid and accelerating pace of innovation across industries can be daunting and unnerving. These days, research and development budgets should allocate funds to technology investments.
Just like our transition from pre-internet to web 1.0 and web 1.0 to web 2.0 and beyond, many companies are overwhelmingly unprepared and unaware of the changing tides. It’s worth noting that simply throwing money at the problem rarely helps — instead, invest in building a cohesive strategy for the modern manufacturing landscape.
1. Modernize Your Tech and Data Stacks
As you invest in modernizing your tech stack, you’ll quickly begin to reap the dividends of a healthy data pipeline — assuming there are no metaphorical leaks in the system. The dividends of a modern tech stack usually come in the form of productivity improvements.
For example, the hours of work your team previously spent manually updating spreadsheets or your CRM can now be automated using activity capture. Not only will activity capture eliminate the wasted time of your team, but it also eliminates the inconsistencies inherent in manual data entry.
2. Unify Your Datasets and KPIs to Track
As your manufacturing processes trend towards complete digitalization, connected devices and sensors will be feeding real-time data into your data pipelines in vast quantities. You might start to wonder if your factory is in the business of producing products or producing data.
Having droves of data is great as it allows you to train machine learning models to turn predictive insights into actionable process improvements. The enabling factor of big data is really data completeness, consistency, and maintenance of a single source of truth.
One of the challenges that you face in digitalization is limiting your purview to the most important key performance indicators (KPIs) to track and focusing on improving on them.
3. Put Your CRM on Autopilot
In the case of most OEMs, manufacturing is only a small part of overall operations. Turning raw materials into a product is one thing, but having a sales team generating demand for that product adds additional complexity. Thankfully, digital transformation is solving these problems as well.
Your CRM, for example, is effectively a data pipeline of your team’s activities, sales opportunities, and more. If you’re not leveraging the latest in CRM technology, such as automatic business activity capture, deal scorecards, leaderboards and more, your digital transformation is far from over.
Automation is poking its helpful head into every process and workflow, including the reduction in your reps’ weekly CRM manual data entry activities, which are extracted away by sales force automation.
4. Leverage The Predictive Powers of AI
Currently, you might be spending your valuable time pulling data reports, digging into analytics, and attempting to hypothesize the cause and effect of performance. With predictive analytics, however, the actionable insights are surfaced for you to spend this time being more strategic and coach your team towards improvement.
Data that was previously locked away in a black box of sorts can now be leveraged to train models on your team’s actual data, and the actionable insights that result are now more accessible than ever before.
5. Performance Management in Manufacturing
Ultimately, the goal of digital transformation is to drive more effective and efficient performance management. With productivity improvements and efficiency optimization being the status quo of the industry, anything to give your team incremental (if not exponential) improvements should be deeply considered.
Leveraging the right technologies to drive growth and improve operational efficiency is likely going to be the margin separating you from the competition. Having a pulse on your team’s performance will be crucial to providing the best possible guidance on how everyone can align on the goal: profitability.
Transforming Your Operations
So what can you do to supercharge your manufacturing and sales processes to drive significant (and predictable) growth?
Manufacturing enterprises in growth mode are adopting and integrating revenue operations and intelligence (RO&I) technology as the new status quo to achieve results while adding predictability and reducing risk. With machine learning surfacing predictive insights in real time, you can align your manufacturing operations with leading indicators and real sales data.
These insights can help optimize your throughput and increase revenue per rep every year. To learn more about how this new category of revenue operations and intelligence can impact your business, check out how People.ai can help manufacturers accelerate digital transformation and stay ahead of change.
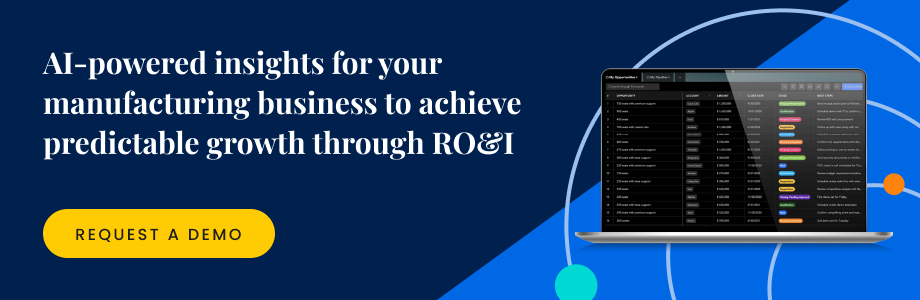